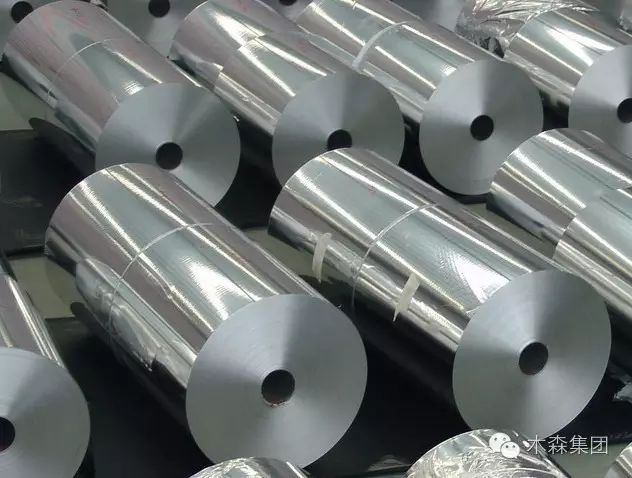
铝箔卷制过程中出现缺陷的处理方法你知道多少?(二)
铝箔轧制由于生产工序较多,加工工艺难度较大,且成品厚度最薄,产生缺陷的概率较其它压力加工高出许多倍,努力减少和消除轧制缺陷是实现安全、优质、高效、低耗生产的关键之一。在轧制过程中可能出现的九大缺陷如下:
5号 边缘裂纹
铝箔表面纵向边缘断裂的情况。严重时可在边缘处看到明显的缺口。
造成边缘开裂的主要原因有以下几点:
a)卷形控制不当,造成铝箔边部产生拉应力;
b)中间退火不充分,金属塑性差;
c) 切料时送料不当,有一边没有切完;
d) 轧制压下量过多;
e) 切边刀不够锋利或调整不当;
措施
1、控制边缘,尽量放松边缘(上弯)。
2、采用轻背张力,低速轧制,可减少裂边。
3、尽可能地切割边缘。
4、选用DC材料而非CC材料。
5.检查切边刀的状况。
6、改进和优化轧制工艺流程。
6号 伯尔
剪切箔的边缘上存在大小不一的毛发状尖刺。
产生毛刺的原因主要有以下几点:
a) 切割时刀片不锋利;
b) 切削刃润滑不当;
c) 切削刃间隙、重叠调整不当;
d) 切边后,铝箔端面有尖刺状铝屑;
f)铝箔在轧制时可能出现切边;
措施
1、更换切刀
2、重新调整切刀
7.形象不佳
因变形不均匀而引起箔面局部起伏的现象,属于型面不良。
根据缺陷所在位置,可分为中波、边波、双肋波和复合波。缺陷在边上的叫边波,缺陷在中波上的叫中波,两者合在一起的叫复合波。既不在中也不在边的叫双肋波。
造成型材形状不良的主要原因有:
a)来料板形质量不良,板材厚度偏差超标;
b)压力调节不平衡,辊型控制不当;
c) 轧制道次压下量不当;
d)辊型不合理;
e) 轧制油喷油量异常;
措施
1、根据来料板形,增加背面拉伸力及产量负荷。
2、输入正确的板形参数。
3、随时注意生产线上的板形,并及时进行调整。
4、若板形仍不能改善,经不断调整后,通知相关人员查找原因。
5、若中途停止生产,复产后板形莫名其妙地变差,可改卷生产。
No.8 非金属压痕
非金属夹杂物压入箔片表面,使表面呈现明显的斑块或长条状黄黑色缺陷。
造成非金属压痕的主要原因有以下几点:
a)轧制工艺设备不清洁;
b) 轧制油不洁;
c) 坯料表面受到非金属压制;
d) 铸锭中含有非金属夹杂物;
措施
1、检查毛坯表面。
2、控制材料尾部,避免尾部摆动。
3、每次转动完毕后,应清洗前后滚轮。
4、定期清洗轧机,擦洗烟罩,确保无油污和污垢。
9号横标
铝箔表面形成的与轧制方向成一定角度的局部致密晶粒,光泽度差,有的呈单条线状,有的呈鱼尾状、人字形。
横痕产生的原因主要有以下几点:
1、轧制道次压下量太大;
2、轧制道次压下量与辊型不匹配,温度不均匀;
3、来料板材有凹凸不平的缺陷或局部有斜纹、人字纹;
4、轧制金属变形抗力过大;
5、卷筒上有斜纹;
6、轧制时润滑不足;
措施
1、提高润滑性。
2、优化道次工艺,减少道次减量。
3、改变轧制工艺参数。
4、如有斜纹则须更换卷筒。